The production of seamless tubes is achieved through two main processes: pilgering and cold drawing. Pilgering involves feeding a hot metal billet into two opposing rollers, or "pilger mills," that compress and stretch it into a seamless tube. The cold drawing process involves pulling a metal wire or rod through a small-diameter die, gradually reducing it in size and length until the final, seamless tube is created.
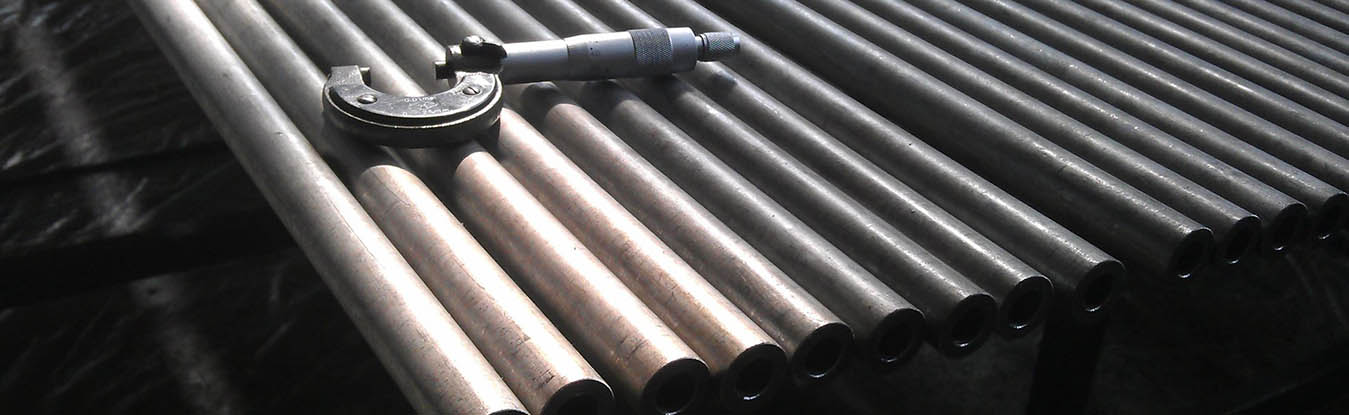
Seamless tubes are frequently used in industries such as aerospace, petrochemical, energy, pharmaceutical, automotive, and manufacturing. They are commonly made from stainless steel, nickel, and titanium, which are known for their excellent strength, corrosion resistance and durability.
Stainless steel is one of the most common materials used in seamless tube production. It is a highly versatile alloy that comes in various grades, such as 304, 316, and 321. Each grade has unique properties that make it ideal for different applications. For example, 304 stainless steel is commonly used in food processing, while 316 stainless steel is preferred in marine environments due to its superior resistance to corrosion.
Seamless stainless steel tubes are also used in the chemical and petrochemical industries, where they are exposed to harsh chemicals and extreme temperatures. Due to the absence of seams, these tubes are less prone to corrosion and stress cracking, making them ideal for demanding applications.
Nickel-based alloys are another common material used in seamless tube production, due to their excellent chemical resistance and high-temperature capabilities. In particular, Inconel and Hastelloy alloys are commonly used in aerospace and chemical industries, where they serve as crucial components in equipment that is exposed to high pressures and temperatures.
Titanium is also used in seamless tubing for its excellent strength-to-weight ratio, high temperature resistance, and exceptional corrosion resistance. It is commonly used in the aerospace industry, where its light weight and strength make it ideal for aircraft components that require precise and reliable performance.
In summary, seamless tubes are the preferred choice for applications where precision, durability, and reliability are critical. The use of stainless steel, nickel, and titanium in their production ensures that they can withstand the most demanding industrial environments, from chemical processing to aerospace engineering. As these industries continue to demand higher performance and efficiency, seamless tubes will remain a crucial component in supporting their operations.